Cabinet manufacturing has evolved dramatically in the last decade. As demand for scalable, high-quality production increases across North America, automated cabinet manufacturing has emerged as the new standard for efficiency, consistency, and speed. Traditional cabinet making relied heavily on skilled labor, but modern buyers—especially those managing multi-unit housing projects, large-scale renovations, or modular kitchen lines—now prioritize precision and repeatability.
This shift is driven by clear economics: automation allows cabinet manufacture and automation processes to scale with fewer defects, faster delivery times, and lower labor costs. In this guide, we’ll explore how companies like Casta Cabinetry in Vietnam are leading the way in cabinet manufacture and automation—combining European technology with high-output capacity and North American compliance standards.
Table of Contents
1. What Is Automated Cabinet Manufacturing?
Automated cabinet manufacturing refers to the advanced production method where digital design software, CNC-controlled machines, robotic systems, and integrated assembly lines work together to produce kitchen and furniture cabinets with minimal human labor. This approach improves speed, consistency, and scalability—three critical factors for contractors and cabinet brands serving large or premium markets.
By eliminating most manual processes, automated cabinet manufacturing not only raises quality standards but also reduces waste, labor costs, and error rates—making it a preferred solution for cabinet brands and furniture suppliers targeting North American projects.
1.1 Core Technologies Involved in Automated Cabinet Manufacturing
Each stage of the automated cabinet manufacturing process relies on specialized equipment that ensures repeatability and precision:
- CNC Routers: Cut cabinet components with ±0.1 mm accuracy, enabling high-speed production of Shaker, slab, and raised-panel designs.
- Edge Banders: Automatically apply PVC, ABS, or wood veneer edging, producing uniform, sealed edges without manual trimming.
- Panel Saws with Nesting Software: Maximize board yield by calculating optimal cutting paths and dimensions.
- Drilling & Doweling Machines: Automate repetitive hinge, shelf pin, and drawer slide installations, ensuring uniform bore placements.
- Integrated CAD/CAM Software: Converts cabinet designs directly into machine instructions, allowing seamless production from digital to physical form.
These technologies work together to form a closed-loop production system—one that minimizes human intervention while delivering consistently high-quality cabinets.
1.2 Key Advantages Over Manual Production
The impact of switching from manual to automated cabinet manufacturing is measurable across multiple production metrics:
Feature | Manual Production | Automated Cabinet Manufacturing |
Cutting Accuracy | ±1.5–2 mm | ±0.1–0.3 mm |
Edge Finish | Varies by worker | Uniform and sealed |
Daily Output | 50–70 cabinets | 200–350 cabinets |
Labor Cost Share | 35–45% | 20–25% |
Error/Rework Rate | 8–12% | <3% |
Batch Repeatability | Low | High consistency |
Automation doesn’t just boost production speed—it brings a new level of consistency and precision. For brands offering modular or RTA cabinets, this control is crucial to ensure every batch matches flawlessly across projects, SKUs, and retail programs.
1.3 Why Automated Cabinet Manufacturing Matters for Global Buyers
Global contractors, wholesalers, and kitchen cabinet retailers rely on speed, reliability, and value. Automated cabinet manufacturing aligns with those needs in several ways:
- Consistent Output Across Projects: With digitally controlled joinery and edgework, there’s little to no variation—ideal for multi-unit housing developments or large retail orders.
- Improved Profit Margins: Reducing material waste and labor overhead makes it possible to maintain competitive pricing without sacrificing quality.
- Reliable Lead Times: Automated production schedules are less prone to disruption, allowing North American buyers to plan inventory and installations with greater accuracy.
Learn more: Lead Times & Supply Chain Resilience: Navigating Potential Disruptions
- Lower Defect Rates: Fewer reworks and quality issues mean fewer returns, warranty claims, and reputational risks for OEM and private-label brands.
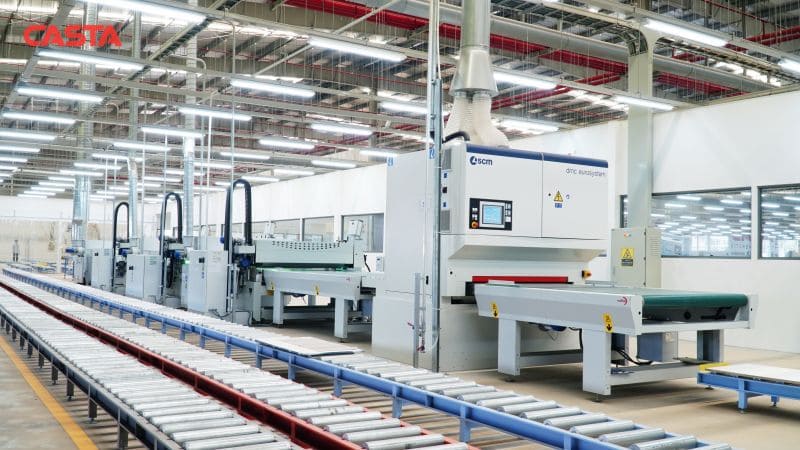
According to the Woodworking Network, companies adopting full automation in cabinet manufacturing experience up to 40% savings in labor costs and a defect reduction of up to 80%, making it an essential upgrade for operations that scale.
In 2025 and beyond, automated cabinet manufacturing is no longer a premium feature—it’s the new standard for scalable, high-quality cabinet production.
2. 5 Benefits of Automated Cabinet Manufacturing for U.S. Buyers
For contractors, cabinet brands, and developers in North America, choosing suppliers that use automated cabinet manufacturing is more than just a productivity decision—it’s a strategic move that improves consistency, cuts costs, and strengthens your ability to deliver on time and within budget.
Below are the five most critical advantages of sourcing from cabinet manufacturers who rely on fully automated systems:
2.1 Superior Precision and Repeatability
Automated cabinet manufacturing eliminates the inconsistencies common in manual cutting and assembly.
- CNC routers and dowel machines achieve part-to-part variation within ±0.3 mm, critical for precision joinery.
- Every panel, hole, and joint is cut based on CAD input, reducing room for human error.
- Repeat orders—even months apart—will yield the same perfect fit, helping brands maintain product consistency across collections.
For projects like multi-unit housing developments, national kitchen cabinet brands, or modular designs with interchangeable parts, this level of accuracy is essential to avoid costly adjustments during installation.
2.2 Faster Turnaround Time for Large Orders
In today’s fast-paced construction and retail landscape, lead time can make or break a project. Automated cabinet manufacturing significantly improves fulfillment speed:
- Factories equipped with HOMAG, Biesse, and SCM automation can run up to 24 hours a day with minimal downtime.
- Multiple orders can be queued and processed simultaneously using integrated CAD/CAM scheduling systems.
- Rapid cabinet assembly and automated packaging systems help reduce production-to-shipping time, allowing orders to reach U.S. job sites on schedule.
For U.S. contractors working on time-sensitive build-to-rent communities or retail cabinet brands managing seasonal launches, automation offers reliable throughput when speed is non-negotiable.
2.3 Cost Efficiency at Scale
While automation requires upfront investment, the long-term savings are substantial—especially for high-volume buyers. Automated cabinet manufacturing lowers production costs in several ways:
- Nesting software improves material yield by optimizing cut paths and reducing board waste.
- Labor cost is reduced by up to 40% since fewer skilled operators are needed on the line.
- Automated edge banding and assembly reduce cycle times per cabinet unit, allowing more cabinets to be produced within the same labor hour.
According to Deloitte’s manufacturing reports, automated operations often deliver cost-per-unit reductions of 15–25% compared to traditional methods—particularly valuable for U.S. buyers looking to balance quality and margin.
2.4 Customization Without Slowing Production
One of the outdated perceptions about automation is that it limits flexibility. In reality, modern automated cabinet manufacturing systems are built for customization at scale.
- Integrated CAD/CAM pipelines allow changes in dimensions, hardware positioning, or finish without manual reprogramming.
- Unique configurations like extra-deep drawers, non-standard heights, or smart cabinet components (lighting, charging ports, locks) are supported directly in the workflow.
- OEM customers can offer personalized SKUs or private-label product lines with ease.
For U.S. brands competing in the premium or semi-custom segment, this is a major advantage: you can deliver tailored features without increasing your lead time or production cost.
2.5 Easier Quality Control and Certification Compliance
Meeting the stringent health, safety, and quality regulations in North America is non-negotiable—and automated cabinet manufacturing simplifies the process of compliance.
- Integrated software tracks each step in production, ensuring that every cut, drill, and assembly meets spec.
- Automated checkpoints flag issues early, reducing the risk of shipping non-compliant or defective parts.
- Digital recordkeeping supports faster audit response and easier documentation for CARB Phase 2, E1, FSC, and ISO certifications.
Learn more: Cabinet certification
This is particularly important for brands distributing across multiple U.S. states or Canada, where local regulations may differ. Manufacturers using automation are better equipped to meet those requirements without delay or added cost.
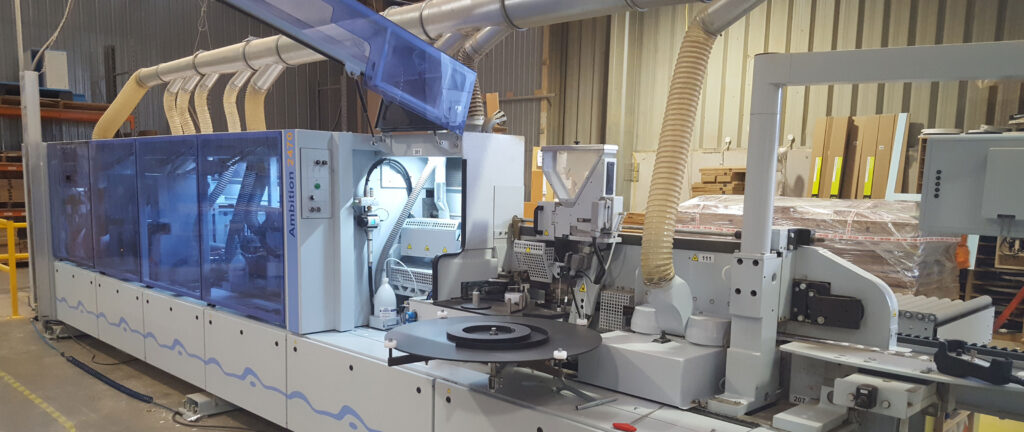
Learn more: Top rated cabinet manufacturers
3. Inside Casta Cabinetry’s Automated Production in Vietnam
Casta Cabinetry stands at the forefront of automated cabinet manufacturing in Vietnam, blending European machinery with intelligent systems to support scalable, high-precision production for international partners. For U.S. contractors and cabinet brands looking to ensure speed, consistency, and regulatory compliance, Casta's factory offers one of the most advanced setups in Southeast Asia.
3.1 Equipment Overview: Built for Scale and Precision
Casta operates out of a 100,000 m² production facility specifically designed to support modern cabinets manufacture and automation workflows. Every key machine on the production floor plays a role in reducing human error and boosting throughput.
- HOMAG CNC Routers: Perform ultra-precise cutting with ±0.2 mm tolerance, crucial for frameless and European-style cabinetry where millimeter-level accuracy defines final fit.
- BIESSE Edge Banders: Deliver seamless edging for high-gloss acrylic, matte laminates, and foil-wrapped finishes, ensuring premium aesthetics across large volumes.
- SCM Saw & Drilling Centers: Use automatic panel feeders and precision-guided blade systems for clean, consistent cuts across MFC, MDF, and plywood substrates.
- Integrated CAD/BIM Workflow: Accepts .dxf, .step, and other architectural files to automate layout planning and production sequencing—critical for commercial and multi-unit residential builds.
All systems feed into a central production management platform, enabling live monitoring, predictive maintenance, and multi-batch scheduling. This ensures that every step in the automated cabinet manufacturing process—from panel cutting to packaging—is traceable and optimized.
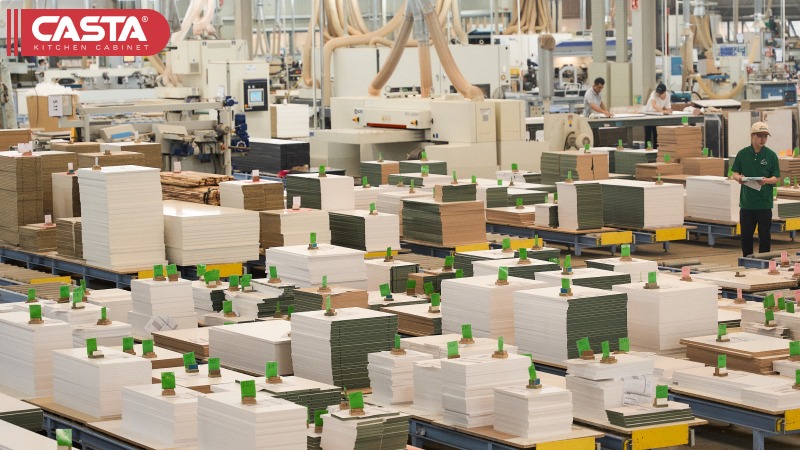
Learn more: Casta’s OEM Manufacturer
3.2 Quality Management System
In any automated cabinet manufacturing setup, precision is only one side of the equation. Casta pairs its equipment with a rigorous, software-enhanced quality management process to ensure defect-free delivery.
- Pilot Runs: Every new order undergoes prototyping and pre-assembly to verify design feasibility, part fitment, and packaging specs before full-scale production begins.
- Inline Quality Control: QR-coded tracking systems and digital measurement tools check for tolerance deviation, part orientation, and assembly alignment in real time—dramatically reducing rework rates.
- Final Export Audits: Prior to shipment, Casta conducts a final visual inspection with independent defect reporting, moisture-level checks, and packaging integrity assessments. All export containers include full documentation for North American customs clearance, including CARB P2 and FSC certifications.
These protocols ensure that even in a high-speed cabinet manufacture and automation environment, craftsmanship and compliance remain uncompromised.
3.3 Health-Safe, Certified Materials
Casta understands that automated precision must be matched with material safety and global compliance—especially for buyers importing into the U.S. and Canada.
- CARB Phase 2 and E1 compliance is standard across all boards and adhesives used in production, supporting low-emission requirements for formaldehyde and VOCs.
- FSC-Certified Substrates are available for environmentally conscious projects or government-regulated housing contracts.
- Core material options include:
- Moisture-resistant MDF (ideal for bathroom vanities or humid climates)
- E0-grade plywood (low-emission structural panels)
- Melamine-faced chipboard (for cost-effective, durable cabinetry)
- Finish options are engineered for seamless integration with automated cabinet manufacturing processes:
- UV-cured lacquer finishes for scratch resistance and clarity
- PVC foil wraps for modern designs with seamless edges
- Thermal-structured melamine for wood grain textures and matte finishes
Every material selected is tested for compatibility with robotic cutting, edge banding, and assembly workflows—minimizing waste and ensuring a consistent final product batch after batch.
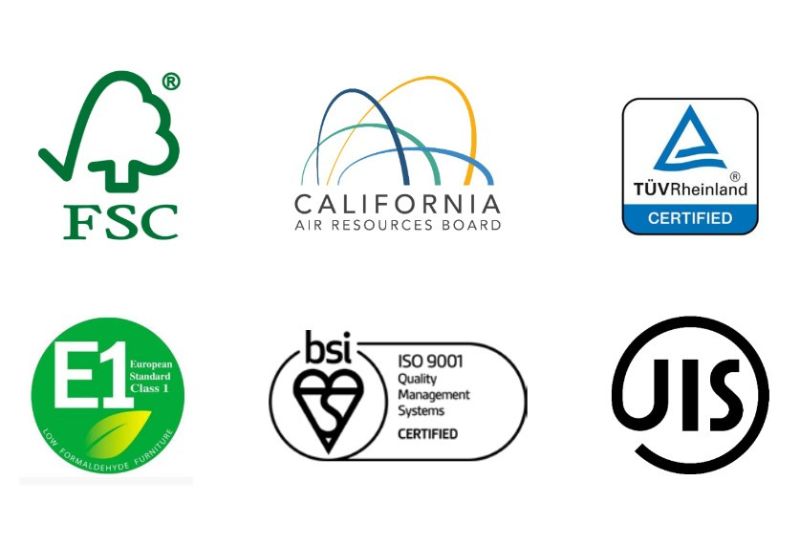
3.4 Common Buyer Concerns—Answered
For many North American contractors and cabinet brands, the shift toward automated cabinet manufacturing—especially overseas—comes with legitimate questions. Casta Cabinetry proactively addresses these concerns through transparent systems and proven performance.
- Will automated cabinet manufacturing reduce design flexibility?
Not at all. Casta’s CAD-integrated production line is built for flexibility. Whether it’s custom drawer sizes, varied hardware placements, or brand-specific finishes, Casta handles short-run customization as efficiently as large-scale uniform builds. - How do I ensure my cabinet specs are correctly followed?
Every order begins with a CAD or BIM file review, followed by a prototype build. Nothing moves to full production without sample approval. Every part is also QR-coded for tracking during the cabinet manufacturing process. - What if there are errors in a large batch?
Inline QC checkpoints and automated deviation alerts catch most issues before they leave the line. Final audits, including moisture content and visual checks, further guarantee that what arrives meets your specs. - Can automated production match U.S. quality standards?
Yes—Casta uses the same machinery brands (HOMAG, BIESSE, SCM) as top-tier U.S. and European manufacturers. The tolerances achieved in automated cabinet manufacturing often surpass manual benchmarks, particularly for frameless and modular designs. - Are the materials safe and compliant for North American interiors?
All materials used meet or exceed CARB Phase 2, E1, and FSC standards. Certificates are included in each export file. You’ll have everything needed for inspections, LEED credits, or green building certifications.
4. Case Study: Supplying 10,000+ Units for U.S. Multi-Family Housing
Project Overview:
Casta Cabinetry partnered with a U.S.-based developer to supply over 10,000 kitchen and bathroom cabinet units for more than 100 multi-family apartment buildings spanning seven states—ranging from Texas to New York.
This project required exceptional consistency across units, rapid turnaround, and full compliance with local cabinetry safety standards. With tight construction timelines and strict quality benchmarks, the client needed a supplier who could scale quickly without compromising on finish, function, or regulatory documentation.
How Automated Cabinet Manufacturing Delivered:
- Modular Layout Precision:
Using integrated CAD/CAM and CNC systems, Casta produced pre-drilled cabinet components based on universal modular layouts. This minimized on-site cutting or drilling and ensured each unit aligned with U.S. appliance specs, plumbing fixtures, and countertop tolerances. - Hardware Pre-Alignment:
Through robotic doweling and pre-inserted connectors, each set of cabinets arrived with hardware perfectly aligned—eliminating time spent adjusting hinges, runners, or lift-up mechanisms during installation. - Just-in-Time Shipment Strategy:
Automated production scheduling enabled batch-based shipments in sync with site progress. Cabinets were packed, labeled by unit/room, and shipped directly to job sites in sequence—avoiding warehouse congestion and reducing handling.
Quantifiable Results from Automation:
Performance Metric | Outcome Achieved |
Installation Time Reduction | -18% (faster fit-outs with modular builds) |
Return/Defect Rate | <1.5% (thanks to automated QC checkpoints) |
Project Lead Time Consistency | Maintained 5–6 week turnaround across all phases |
Developer Satisfaction | Repeat orders placed by 5 additional clients |
This case proves how automated cabinet manufacturing can transform large-scale construction logistics by eliminating guesswork and reducing downstream delays. Rather than relying on traditional millwork, which can vary by carpenter and site condition, automation provided uniform cabinetry that performed consistently—regardless of geography or team.
Why It Matters for U.S. Contractors and Developers:
- Fewer On-Site Adjustments: CNC-cut parts and factory-installed hardware reduced labor costs during install.
- Easier Quality Inspection: Uniformity made it faster for site supervisors to sign off on fit and finish.
- Repeatability for Expansion: Future buildings could replicate layouts without new design time or onboarding delays.
- Trusted Compliance: All cabinets included CARB P2, E1, and FSC documentation required for building code approvals and environmental assessments.
As more developers shift toward offsite construction and lean project management, automated cabinet manufacturing offers a dependable foundation for scalable growth.
Learn more: Casta’s Outstanding International Projects
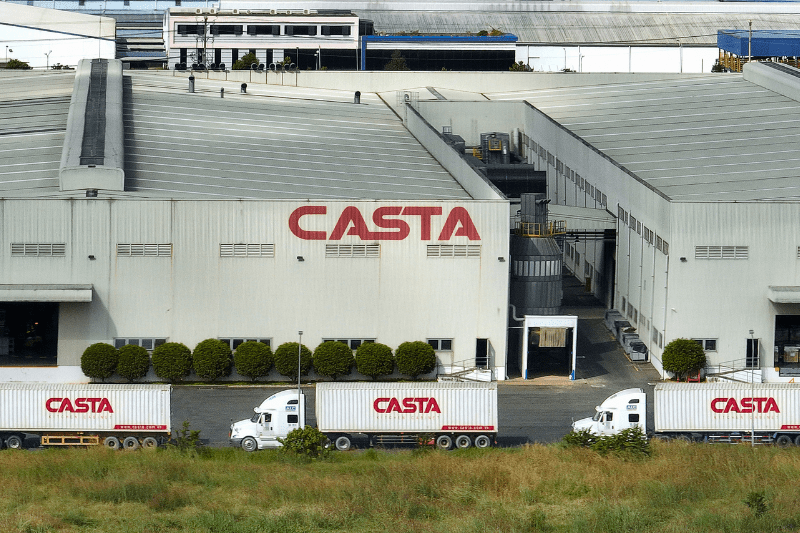
5. Enhancing Custom Design Through Automation
One of the key strengths of automated cabinet manufacturing lies in its ability to support mass customization without disrupting production efficiency. For North American brands and contractors seeking tailored designs across different project tiers—from luxury builds to budget-conscious multi-family developments—automation bridges the gap between speed and flexibility.
Design Customization Features Enabled by Automation
- Pre-Loaded Finish Libraries
Casta’s factory maintains an extensive digital library of pre-approved finishes, including matte, gloss, woodgrain, and anti-fingerprint textures. These are mapped directly into the CAD/CAM systems, enabling seamless finish matching across cabinet lines. This means custom designs can be turned around faster—without starting from scratch.
- Motion Hardware Integration
The automated workflow accommodates advanced hardware options such as:
- Touch-to-open systems for handleless designs
- Soft-close runners and hinges for a premium tactile feel
- Servo-driven lift-up doors, ideal for high-end kitchens and compact urban spaces
These features are built into the design file and processed through machines programmed to match exact hardware specs—whether you use BLUM, Hettich, or DTC. The result is a smooth, standardized fit that aligns with global expectations for functionality and style.
- Flexible Cabinet Architecture
Whether you need inset drawers, L-shaped base cabinets, or integrated smart locks, automated cabinet manufacturing enables rapid layout changes through digital prototyping. Once approved, these changes are immediately implemented across production batches with high accuracy and no downtime.
- Flat-Pack or Pre-Assembled Options
Automated doweling, gluing, and screwing stations make it easy to toggle between flat-pack units for RTA brands or fully assembled modules for commercial builds. This adaptability eliminates manual bottlenecks while serving a broader customer base.
- Fast Prototyping for OEM Clients
For cabinet brands developing exclusive collections, automation allows for fast prototyping with real-world simulations. Clients receive pre-production samples with millimeter-perfect detailing—ready for photography, showrooms, or pilot installs.
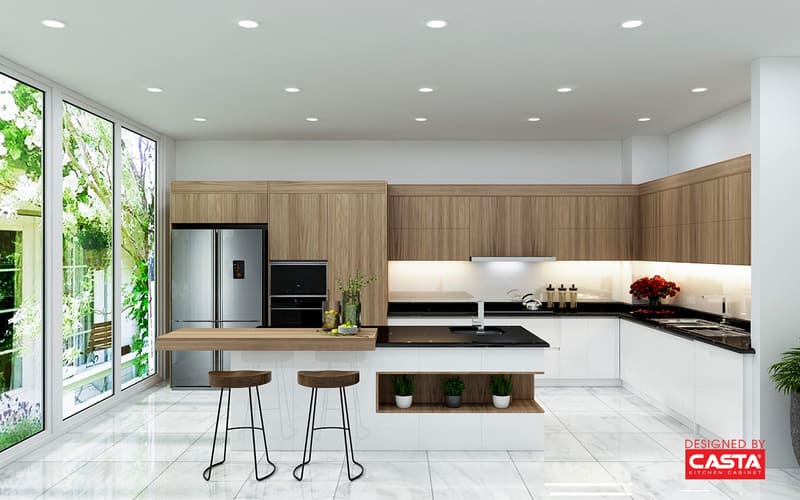
6. Logistics & Export Support for North American Clients
One of the key advantages of sourcing through Casta Cabinetry’s automated cabinet manufacturing process is its built-in export-readiness. The factory floor isn’t just optimized for speed and consistency—it’s engineered to handle every step of delivery to North America. From documentation to protective packaging, the process ensures you receive your cabinets on time, damage-free, and fully compliant with U.S. and Canadian regulations.
Before Shipping: Export Readiness at the Factory Level
Standardized Lead Times
- 25–40 days door-to-door from Vietnam to major North American ports like Los Angeles, Houston, and Savannah
- Faster processing vs. Chinese ports, with less congestion and shorter customs hold times
- Reliable for large-scale project rollouts and retail launches with fixed deadlines
Compliance & Documentation Package
Every container produced through Casta’s automated cabinet manufacturing system ships with a full export file, tailored for U.S./Canada:
- CARB Phase 2 compliance: Required for indoor cabinetry across U.S. states
- E1 certification: Accepted in both Canada and the European Union
- FSC Mix-Credit certification: Proof of responsibly sourced wood
- Material Specification Sheets: Lists core material, surface finish, and hardware per model
- Packing List & Commercial Invoice: Structured for customs brokers and duty review
These documents reduce customs delays, support inspection clearance, and give you all the data needed for inventory and quality control.
Pre-Shipping Packaging Protocols
Components manufactured via automation are packaged with container shipping in mind:
- Moisture-Proof Protection: Laminated liners and corner guards defend against ocean humidity
- Reinforced Cartons: Double-wall boxes with internal bracing preserve shape under load
- Barcode Labels: SKU-level scannable labels for easy warehousing and installation routing
- Flat-Pack Optimization: CNC nesting reduces volume, lowering per-unit freight costs by up to 15%
During Shipping: Fulfillment Flexibility Built for Contractors and Brands
Shipping Modes
- Full Container Loads (FCL): Most cost-effective for large orders; Casta provides optimized stacking plans
- Split Loads / Consolidated SKUs: Combine multiple projects or phases in one shipment
- Assembled or Flat-Pack Delivery: Choose between factory-assembled cabinets or ready-to-assemble (RTA) format based on install team preference
Delivery Coordination Services
- Just-in-Time Shipping: Schedule arrivals by project phase, avoiding costly jobsite storage
- Freight Forwarding Support: Includes coordination with U.S. port agents, trucking, and unloading
- End-to-End Visibility: Status updates from factory to final delivery point
Why It Matters
In the North American market, delays, damage, or compliance gaps can add weeks and thousands in cost. Casta’s vertically integrated automated cabinet manufacturing and logistics process reduces that risk—ensuring your orders are accurate, export-compliant, and install-ready the moment they arrive.
7. Why North American Buyers Choose Casta Cabinetry
For U.S. and Canadian contractors, developers, and cabinet brands, selecting the right overseas partner comes down to more than price—it’s about trust, precision, and long-term support. Casta Cabinetry stands out among Vietnamese suppliers by combining automated cabinet manufacturing with tailored OEM services designed specifically for the North American market.
Scalable Production with Precision
- Capacity: Casta’s facility spans over 100,000 m² and houses a fully automated production line capable of outputting up to 10,000 cabinets per month. This scale allows buyers to place large, multi-phase orders with confidence—whether it’s 500 kitchens for a housing development or weekly pallet drops for a retail chain.
- Smart Line Configuration: Each stage of the automated cabinet manufacturing process is optimized for efficiency, from robotic panel cutting to edge banding and dowel insertion. As demand grows, Casta can scale production while maintaining batch consistency.
Compliance with North American Standards
- CARB Phase 2: Every cabinet produced meets the California Air Resources Board’s stringent formaldehyde emissions standard—now widely accepted as a benchmark across the U.S.
- E1 Compliance: Ensures European-standard emissions, which are also adopted in many Canadian markets.
- FSC Certification: All wood and board materials are sourced responsibly, verified by the Forest Stewardship Council—making Casta a fit for environmentally conscious projects.
- All compliance documentation is integrated directly into the company’s automated cabinet manufacturingsystem, ensuring no delays during customs or inspections.
Clear Communication & OEM Expertise
- English-Speaking Project Team: From initial CAD revisions to shipping documents, every touchpoint is handled by a dedicated export team fluent in English and experienced in North American build requirements.
- OEM Branding Options: Casta offers logo stamping, barcoding, and custom labeling—ideal for private-label cabinet lines or retail packaging.
Sample Use Cases (2025):
- U.S. Retailer: 3,200 cabinet sets with stamped logo + SKU labels for flat-pack eCommerce.
- Canadian Brand: 180 showroom kits with QR-coded guides for easy RTA setup.
- Multi-Family Builder: 600 units labeled per room for phased jobsite delivery.
This OEM flexibility ensures a seamless brand experience from factory to install.
Quality Assurance & Reliability
- Pre-Production Prototypes: Before large-scale manufacturing begins, Casta provides working samples that reflect the exact specs of the final cabinet line—including finish, hardware, and joinery.
- Automated QC Stations: Integrated scanners, sensors, and software checkpoints inspect every piece during the automated cabinet manufacturing process—minimizing human error and catching defects before packaging.
- Installation Guidance: For multi-unit or builder-grade projects, Casta provides exploded diagrams, QR-linked videos, and labeling systems that simplify on-site assembly.
Partnership-Driven Approach
North American clients appreciate that Casta Cabinetry isn’t just a supplier—it’s a long-term partner. With a vertically integrated production floor, transparent communication, and a relentless focus on quality, Casta ensures that your cabinets arrive on time, on spec, and ready to install.
Learn more: Casta’s Ideal Custom Cabinets
8. Final Takeaway: Automation Reduces Risk & Improves Value
Automated cabinet manufacturing is no longer a luxury—it’s the new standard for efficiency, consistency, and competitive edge in today’s cabinet industry. For North American contractors, furniture brands, and kitchen cabinet retailers, automation offers a reliable way to scale without compromising quality or delivery timelines.
At Casta Cabinetry, every order is backed by precision-driven automated cabinet manufacturing systems, certified materials, and export-ready packaging. Whether you're launching a new modular kitchen line or outfitting multi-family developments, automation lowers the risk of defects, accelerates turnaround, and strengthens your bottom line.
When sourcing matters, choose a partner that combines advanced machinery, expert OEM support, and a deep understanding of North American compliance standards—choose Casta.
9. FAQ: Automated Cabinet Manufacturing
Can automated cabinet manufacturing support complex OEM requests?
What types of documentation are provided?
Are small batches possible with automated systems?
Does automation support smart cabinet components?
How do I get started sourcing from Casta Cabinetry?
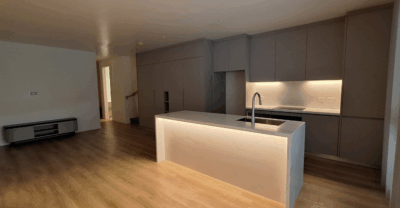
Where to Buy Manufactured Home Cabinet Doors
Cabinet is one of the most critical components in manufactured homes, and selecting the right manufactured home cabinet ...
08/29/2025 | David Nguyen
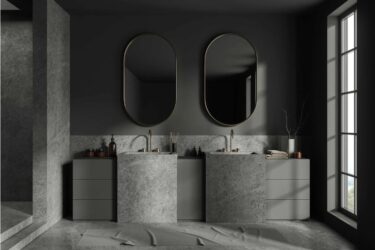
Where to Source Wholesale Bathroom Vanities: Top Suppliers ...
Sourcing wholesale bathroom vanities isn’t just about slashing per-unit costs—it’s about streamlining your entire projec...
08/23/2025 | David Nguyen
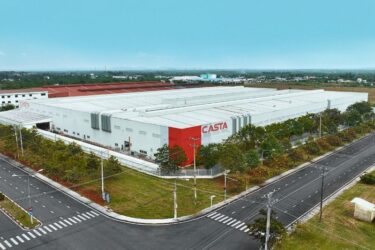
Best Furniture Manufacturer in Vietnam
A furniture manufacturer in Vietnam offers North American contractors and cabinet brands a reliable solution for high-vo...
08/21/2025 | David Nguyen
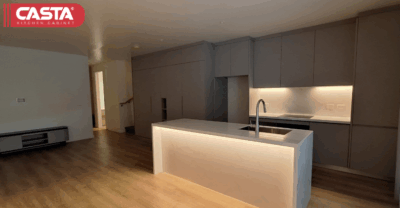
Next-Gen Cabinets for Manufactured Homes: Trends, Where to B...
In recent years, the role of cabinets for manufactured homes has evolved from basic “builder grade” components into high...
08/15/2025 | David Nguyen
Contact us
Casta is always ready to listen and answer all customers' questions
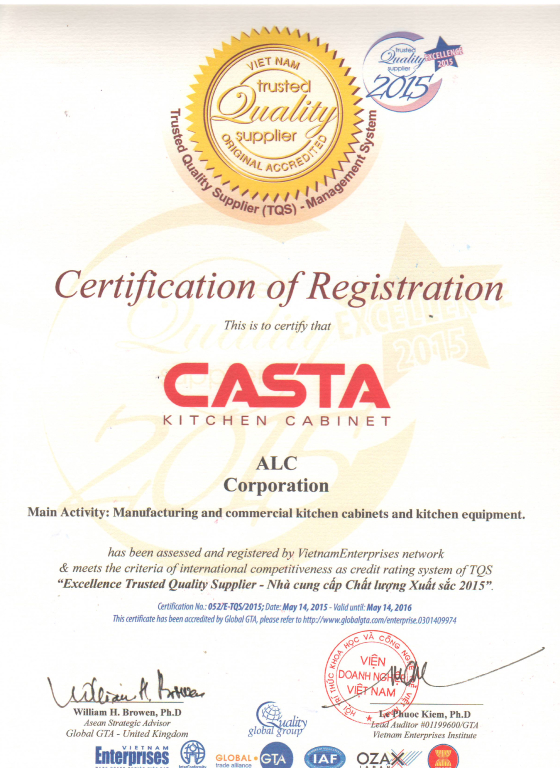
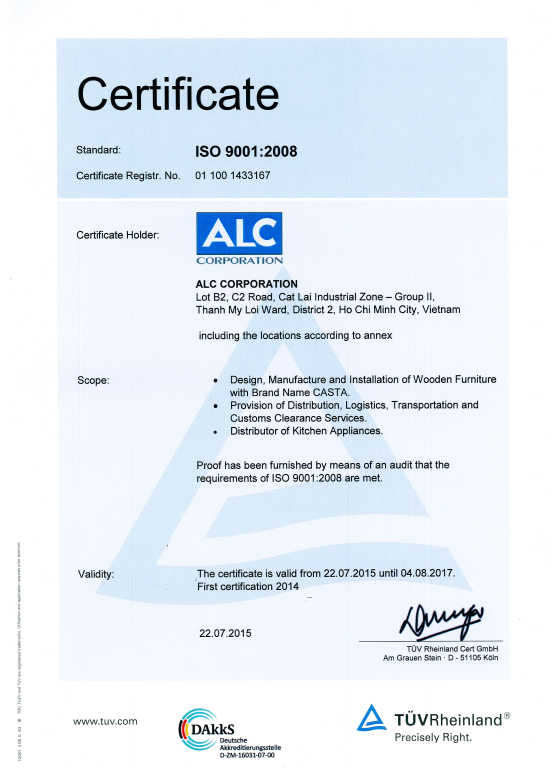
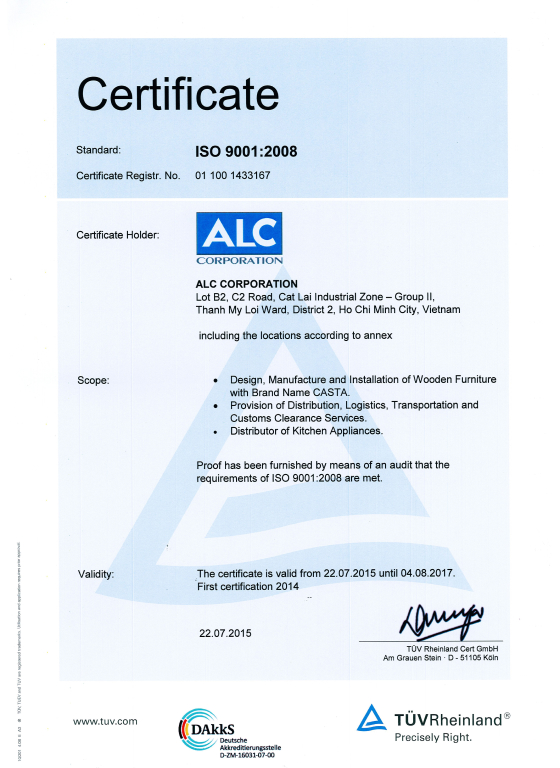