Today’s North American contractors, furniture brands, and developers demand more from cabinet manufacturers: speed, accuracy, customization, and compliance. Understanding the full cabinet manufacturing process is no longer a technical luxury—it’s a competitive necessity. Whether you’re sourcing framed or frameless kitchen cabinets, delays, inconsistencies, or subpar finishes can ruin project timelines or damage brand reputation.
That’s why it pays to understand each stage of the kitchen cabinet manufacturing process. From raw board selection to final shipment, every step has implications for cost, finish quality, durability, and client satisfaction.
Casta Cabinetry—a Vietnam-based OEM manufacturer with over 100,000 m² of production space—serves some of the most demanding North American cabinet brands. Using fully automated European equipment and strict export controls, they ensure precision, speed, and health-safe quality.
In this article, we walk through the complete cabinet manufacturing process flow and show how customization, certification, and logistics align to serve both contractors and cabinet companies.
1. 7-Step Cabinet Manufacturing Process Flow
A well-controlled cabinet manufacturing process ensures quality, consistency, and timely delivery—especially when serving the demanding North American market. The following seven stages outline the cabinet manufacturing process flow used at Casta Cabinetry, from material selection to final export.
1.1 Material Selection & Certification
The cabinet manufacturing process begins with carefully choosing the right substrate, as it impacts durability, finish compatibility, and long-term performance.
Common Substrates by Cabinet Type:
- Framed cabinets: Typically use solid wood or plywood for face frames, and MDF or plywood for the cabinet box.
Example: A heritage-style remodel in Georgia used birch plywood face frames with MDF panels for smooth-painted Shaker doors.
- Frameless cabinets: Constructed using moisture-resistant MDF, laminated particleboard, or high-grade plywood for clean panel-based construction.
Example: A modular apartment project in Texas sourced frameless kitchen cabinets made with MR MDF and laminated particleboard to maximize space and reduce cost per unit.
Learn more: Frame vs Frameless cabinets
Certifications Required in Global Cabinet Manufacturing:
- CARB Phase 2: California standard for formaldehyde emissions, now widely accepted across the U.S.
Use case: Required for all cabinets in a 200-unit California senior housing project to meet state regulations.
- E1: European emission benchmark, commonly required by Canadian and European buyers.
Use case: A custom kitchen line exported to Quebec needed E1-compliant MDF to pass local residential codes.
- FSC Mix-Credit: Certifies responsible forestry practices—often required for green building credits.
Use case: A boutique hotel chain in Vancouver used FSC-certified plywood boxes for LEED certification.
Fit-to-Project Tip:
- Frameless cabinet systems are ideal for modern kitchens where space efficiency and minimal lines matter.
Example: Frameless units made with high-gloss acrylic MDF were installed in a Manhattan micro-apartment project to reflect light and expand the sense of space.
- Framed cabinets are often preferred for traditional, shaker, or transitional aesthetics that require face-frame styling.
Example: A New Jersey custom home featured maple face frames with stained finishes to complement a craftsman kitchen design.
1.2 CNC Precision Cutting
Precision cutting is a cornerstone of the cabinet manufacturing process flow—affecting everything from joinery alignment to surface finish.
CNC Systems Used:
- HOMAG and Biesse CNC routers: Used at Casta Cabinetry for nesting panels with tolerances as tight as ±0.1 mm.
- Optimized software ensures both frameless cabinet manufacturing process and framed layouts are cut accurately and with minimal waste.
Cutting Approaches by Cabinet Type:
- Framed cabinets: Face frames are cut separately and joined using mortise/tenon or pocket screw methods.
- Frameless cabinets: Entire panels are nested and cut together, including all hinge and dowel bores—ideal for fast, repeatable production.
Real Use Case:
A Texas-based apartment project used standardized frameless cabinets from Casta. CNC-precise parts reduced on-site fitting issues by 30%, while the consistent sizing allowed installers to complete 8–10 units per day.
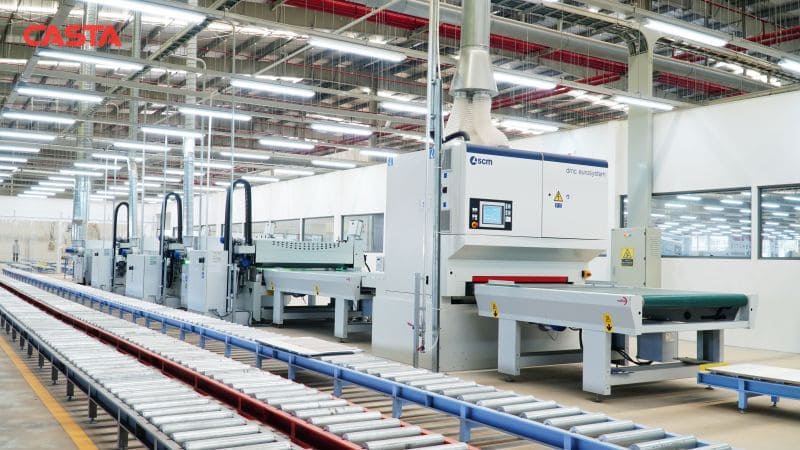
1.3 Drilling and Joinery Preparation
After cutting, the next step in the cabinet manufacturing process is joinery preparation—ensuring smooth assembly and hardware integration.
Drilling & Joinery Systems:
- Frameless systems: Utilize the 32mm European system, with pre-drilled holes for dowels, cam-locks, or Confirmat screws. This setup supports fast, flat-pack-friendly assembly with precise part alignment.
- Framed systems: Require additional hinge cup boring and face-frame-specific mounting patterns, especially for overlay or inset door setups.
Common Joinery Options & When to Use Them:
- Cam-lock + dowel systems:
- Ideal for RTA (Ready-to-Assemble) cabinets shipped flat-packed.
- Easy to install with minimal tools, suitable for DIY or fast field assembly.
- Caution: If used without glue, cam-locks may loosen after 2–3 years, especially in high-use kitchen zones.
- Minifix + dowel connectors:
- Offer better re-tightening ability than standard cams.
- Common in European-style cabinets needing transportability and structural rigidity.
- Dowel + glue:
- High-strength joinery used in premium cabinets or pre-assembled builds.
- Offers excellent resistance to joint movement over time.
- Example: A retail cabinet brand in Canada required glued dowels for showroom cabinets to withstand repeated door pulls and minimize service claims.
- Confirmat screws:
- Used in laminated particleboard or MDF cabinets where mechanical hold is prioritized over aesthetics.
- Standard in many budget RTA cabinet lines sourced for multi-family or student housing.
Design Insight:
- Frameless cabinets rely heavily on concealed joinery—helping maintain a sleek, minimalist look. These hidden fasteners also make it easier to align components quickly on-site.
- Framed cabinets, in contrast, may feature visible hinges or decorative hardware, which is pre-drilled during this phase to avoid misalignment during installation.
Proper joinery planning during this stage of the cabinet manufacturing process directly impacts long-term cabinet performance, ease of installation, and customer satisfaction.
1.4 Edge Banding & Surface Finishing
This critical phase of the cabinet manufacturing process enhances both the aesthetic value and structural resilience of the product. It’s especially vital in frameless cabinet manufacturing processes, where clean, sealed edges are fully visible and exposed to daily wear.
Edge Banding Methods:
- Laser or PUR (Polyurethane Reactive) Edgebanding:
- Creates seamless, moisture-sealed joints—ideal for modern matte or glossy acrylic finishes.
- Highly resistant to humidity, peeling, and bug intrusion, making it a preferred option for frameless cabinets in urban or coastal homes.
- Melamine, PVC, ABS Edgebanding:
- Cost-effective, durable, and color-matched for standard kitchen or vanity cabinets.
- Properly sealed edges offer basic water resistance and prevent insects or dust from entering panel joints.
- Frequently used in high-volume RTA cabinet lines for apartments and residential developments.
Finishing Options by Cabinet Type:
- Frameless Cabinets:
- Require smooth, flawless edge finishes due to their exposed construction.
- Poor banding shows immediately in frameless systems, making precision application essential for market-ready results.
- Framed Cabinets:
- Edge banding is typically applied only to interior surfaces (e.g., shelf edges, interior panels), as the face frame conceals outer edges.
Surface Finishing Techniques:
- Melamine Wrapping:
- Used for cost-effective production of RTA cabinet panels.
- Offers water-resistant and bug-repellent surfaces when paired with tight edge sealing.
- UV-Cured Acrylic Lacquer:
- Delivers a high-gloss, scratch-resistant finish for premium kitchen cabinets.
- The anti-yellowing, anti-fingerprint, and low-VOC properties make it ideal for luxury or health-conscious builds.
- Thermofoil Wrapping:
- Applied to MDF doors needing raised profiles or detailed embossing.
- The sealed surface resists moisture, bugs, and warping, making it well-suited for high-humidity environments like kitchens and bathrooms.
Integrating these methods into the cabinet manufacturing process not only improves product durability and aesthetics but also supports export readiness for demanding North American markets where quality expectations and environmental exposure vary widely.
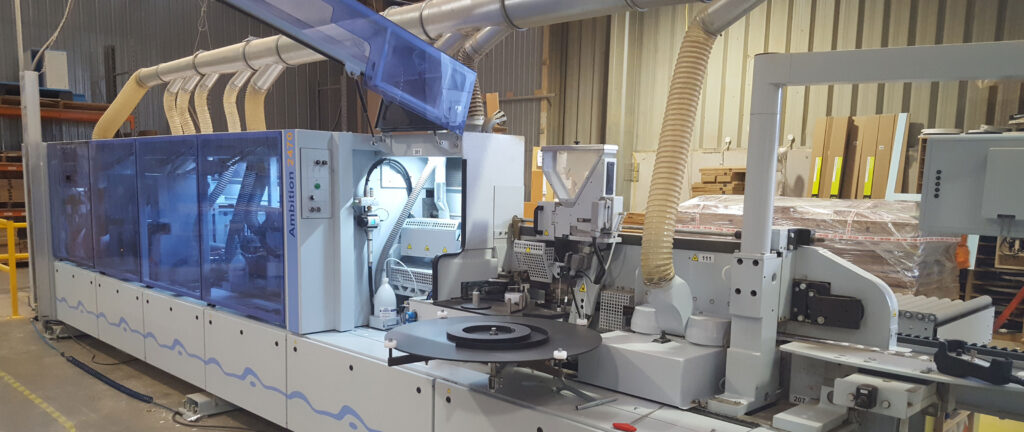
1.5 Assembly or Knock-Down (KD) Prep
This step determines how the cabinet reaches its final form—either as a pre-assembled unit or a flat-packed kit for on-site assembly.
Options Based on Manufacturing Type:
- Frameless KD: All pieces are barcoded with QR labels and packed flat for export.
- Framed Assembly: Face frames are glued or screwed in-house, ensuring square alignment and tight joins.
Integrated Hardware:
- Soft-close hinges (e.g., BLUM, Häfele)
- Push-to-open drawer tracks
- Full-extension undermount slides
Relevance to Buyers:
For brands focused on the custom cabinet manufacturing process, offering both KD and pre-assembled formats allows for scalability and flexibility.
1.6 Final Finishing
The finishing phase is often the most visible part of the kitchen cabinet manufacturing process, where color uniformity, texture, and gloss are perfected.
Available Finishes:
- Matte or high-gloss UV lacquer
- PET laminate with anti-fingerprint surface
- Real wood veneer matched to grain patterns
Styling Considerations:
- Frameless: Uniform edge banding, consistent sheen across doors and carcasses
- Framed: Seamless color/stain transitions between face frame and doors are essential
This step is crucial for brands wanting to develop showroom-ready SKUs with a polished appearance that speaks to quality.
1.7 Packaging, Certification & Export
The final step in the cabinet manufacturing process ensures that every order arrives safely, certified, and ready for distribution.
Packaging Includes:
- Moisture-resistant wrap
- Corner cushions and foam spacers
- Labeling per unit, per room, or per project phase
Documents Supplied:
- Material Safety Data Sheets (MSDS)
- FSC, E1, CARB Phase 2 certifications
- Bill of Lading and fumigation certificates
Lead Times:
- West Coast USA: 25–30 days
- East Coast USA: 30–40 days
Export Tip for Brands:
A smooth cabinet manufacturing process flow from start to finish means fewer customs issues, lower damage rates, and faster install schedules.
Learn more: Top rated cabinet manufacturers
2. Inside Casta’s Sales & Manufacturing Pipeline
The success of any project depends not just on materials or machinery—but on a well-structured cabinet manufacturing process from the first drawing to final delivery. At Casta Cabinetry, every step is engineered to meet the expectations of contractors, cabinet brands, and developers across North America.
Below is an overview of how our end-to-end pipeline supports high-volume, custom, and repeatable production.
2.1 Sales Process for North American Clients
Casta’s cabinet manufacturing projects begin with a transparent and efficient sales pipeline. Our process is built to ensure every kitchen or furniture cabinet meets specification, cost targets, and schedule—all without surprises.
Sales Process Steps:
- CAD or PDF drawings submitted: Clients can send concept layouts, full elevations, or even rough sketches. We also support BIM and SketchUp files for collaborative modeling.
- Value-engineering proposal: Based on design intent, we offer matched materials, finishes, and joinery methods optimized for both cost and compliance.
- Sample door or panel shipped: A physical mock-up is shipped within 7–10 business days for validation—critical for visual review and stakeholder approval.
- Contract & milestone schedule signed: A full production timeline is mapped, including approvals, cutting, assembly, finishing, packing, and export.
This early-stage workflow helps streamline the entire kitchen cabinet manufacturing process, avoiding redesigns or change orders mid-production.
2.2 Manufacturing Overview
At Casta’s 100,000 m² factory in Vietnam, the cabinet manufacturing process is largely automated, combining European machinery with lean production principles. This enables reliable output for everything from multi-family developments to OEM brand lines.
Key Manufacturing Highlights:
- 90% automation across CNC routing, panel drilling, and edge banding—delivering precise and consistent part quality across every cabinet batch.
- ERP-integrated tracking down to individual parts and SKUs, ensuring each cabinet component is traceable and production status is always up to date.
- 3-stage QC (Quality Control):
- Cut-check: Post-CNC validation for dimension, label, and hole alignment.
- Assembly-check: Fit and hardware alignment are reviewed before pre-packing.
- Pre-pack check: A final verification ensures correct labeling, accessories, and moisture protection.
Each step of the cabinet manufacturing process flow is fully documented to reduce errors and support reordering with the same specifications—even months later.
2.3 Logistics Support
Shipping is not an afterthought—it’s integrated into the custom cabinet manufacturing process from day one. Casta’s logistics and export support is purpose-built for North American importers who need fast, damage-free delivery without delays at port.
Logistics Capabilities:
- Sea freight in full 20-ft or 40-ft containers: Standard lead time is 25–40 days, depending on destination coast.
- Consolidated shipments: Combine multiple cabinet models, sizes, and hardware SKUs in the same container to optimize space and reduce per-unit freight cost.
- Split delivery option: Large projects can request phased shipping by floor, building, or installation stage—ideal for hospitality and multi-site developments.
All packaging in the cabinet manufacturing process includes barcoding, edge protection, and moisture-resistant wrap. Whether you’re ordering for 50 units or 5,000, Casta ensures your product is install-ready when it lands.
Learn more: Lead Times & Supply Chain Resilience: Navigating Potential Disruptions
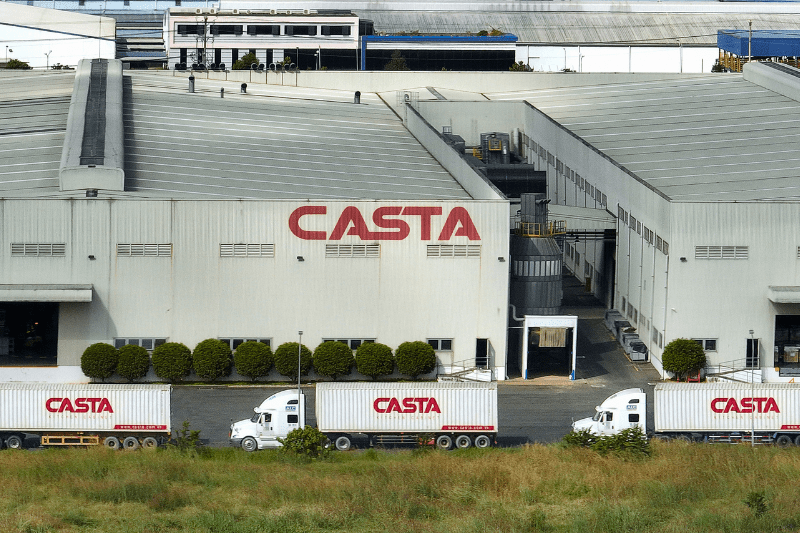
3. Case Study: California Multi-Family Project
Real-world application of a well-executed cabinet manufacturing process helps demonstrate the true value of precision, planning, and product consistency. This California-based project highlights how Casta Cabinetry delivered over 2,000 cabinets with zero product defects, tight turnaround, and long-term client satisfaction.
3.1 Client Overview
A California-based residential developer required over 2,000 frameless cabinets for a fast-moving multi-family housing project. They sought a supplier with a streamlined cabinet manufacturing process that ensured consistency, emission compliance, and cost control.
Key Challenges:
- Inconsistent quality from prior vendors disrupted job-site installs.
- Lack of certified materials jeopardized CARB Phase 2 compliance.
- On-site adjustments increased labor due to poor joinery.
- U.S. suppliers met standards but exceeded budget limits.
Casta Cabinetry’s automated cabinet manufacturing process—from CNC cutting to pre-labeled packaging—delivered repeatable precision and certification-ready documentation, solving both cost and compliance issues..
Project Requirements:
- Cabinet Type: Frameless Euro-style kitchen and vanity cabinets
- Material: Moisture-resistant MR MDF with matte white acrylic finish
- System: 32mm hole system for hardware flexibility and rapid assembly
- Format: Knock-down (KD) flat-pack format for efficient on-site installation
The client chose Casta due to our end-to-end kitchen cabinet manufacturing process that ensured tight tolerances, timely delivery, and full export documentation.
3.2 Execution Highlights
To meet the high expectations of the client, Casta deployed a structured and fully digitized cabinet manufacturing process flow. Using a combination of CAD/CAM integration, automation, and smart packaging logistics, the factory team was able to batch-produce all units with consistent quality.
Manufacturing and Export Highlights:
- CNC Nested by Apartment Unit: Panels were cut, drilled, and barcoded in groups assigned to specific apartments, simplifying delivery, unloading, and installation.
- QR-Coded Labels: Every component was tagged with QR codes linking to its installation location, reducing on-site sorting time by over 40%.
- Project-Based Packaging: Cabinets were packed floor-by-floor and unit-by-unit with moisture barrier wraps, foam padding, and impact protection for long-haul shipping.
- Certifications Supplied: Each container included full export documentation—CARB P2, FSC, E1 compliance, fumigation certificates, and MSDS for coatings.
This stage of the cabinet manufacturing process ensured that the assembly team in California could install the units rapidly with minimal rework or confusion.
3.3 Outcomes
The impact of a well-coordinated custom cabinet manufacturing process was immediately evident on the ground. The entire containerized shipment arrived in excellent condition, thanks to both robust packaging and accurate batching.
Final Results:
- Total Shipped: 6 full containers
- Lead Time: 32 days from production sign-off to U.S. West Coast port
- Product Issues: 0 reported damages or defects
- Client Feedback: Positive experience led to a new 2-year rolling supply contract
By following a consistent and scalable cabinet manufacturing process, Casta was able to not only meet but exceed client expectations. The developer noted that installation labor was significantly reduced due to QR-coded organization and fit precision.
Learn more: Casta’s Outstanding International Projects
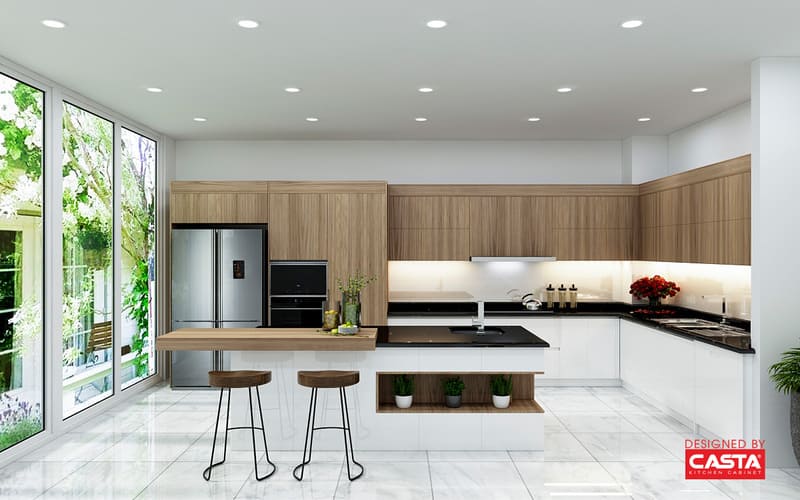
4. Framed vs. Frameless Cabinet Manufacturing Process
Choosing between framed and frameless designs is a foundational decision in the cabinet manufacturing process—one that directly affects aesthetics, cost, assembly, and target customer appeal. Understanding how each construction method impacts manufacturing steps helps buyers, contractors, and brands make informed sourcing decisions.
Feature | Framed | Frameless |
Structure | Built with a solid wood face-frame attached to the cabinet box | Constructed from full-panel sides without a front frame |
Aesthetic Style | Traditional or transitional looks, often stained or painted | Sleek, modern appearance with full-overlay doors |
Manufacturing Setup | Longer setup due to frame assembly and separate drilling patterns | Faster CNC nesting with all panels cut and drilled at once |
Production Speed | Slower due to additional face-frame assembly steps | Faster due to simplified geometry and fewer assembly steps |
Cost | Higher per unit due to labor and material for frame | 8–12% lower cost on average—optimized for bulk orders |
Customization Flexibility | Requires custom face frame adjustments for size/fit | Easily modified with CAD for various drawer/door layouts |
Ideal Project Types | High-end custom homes, boutique retail, or luxury kitchens | Multi-family housing, rental units, or modular kitchen lines |
Typical Margin (U.S. Market) | 25–40% on high-end retail price | 15–30%, depending on scale and finish |
4.1 Structural Differences in the Cabinet Manufacturing Process
In a framed cabinet manufacturing process, face frames are built from solid hardwood and attached to the cabinet box before drilling and edge finishing. This adds time and complexity but offers a rigid structure that supports inset doors and exposed hinges.
In contrast, the frameless cabinet manufacturing process uses panel-based construction, which allows for faster CNC routing and more consistent surface finishes. It’s also easier to implement flat-pack (KD) options, as the assembly is straightforward and parts are standardized.
4.2 Buyer Recommendations
For Contractors
- Frameless cabinets are ideal for apartments, student housing, and other volume-driven projects. Their fast assembly and cost savings make them perfect for tight schedules.
- Framed cabinets work better for luxury homes or custom remodels where craftsmanship and premium materials are selling points.
For Cabinet Brands
- Use frameless cabinets when launching modern product lines aimed at urban markets.
- Choose framed cabinets to expand into heritage or Americana-style collections.
For Retailers and Distributors
- Frameless cabinets are best-suited for RTA (ready-to-assemble) or flat-pack retail programs due to easier packaging and universal hardware compatibility.
- Use framed cabinets in showrooms or demo kitchens to highlight traditional design and build quality.
Margin & Consumer Preference Insight
- Frameless cabinets offer higher volume, lower cost, and consistent quality—making them ideal for developers, hospitality groups, and budget-conscious consumers. Brands can achieve 15–30% gross margin depending on finish and hardware selection.
- Framed cabinets attract clients willing to pay for authenticity and visual detailing. Despite the higher manufacturing cost, retail markups reach 35–40% in premium kitchen lines due to perceived quality and craftsmanship.
Learn more: Sourcing Cabinets and Furniture from Vietnam: Your Ultimate Guide
Choosing the right structure at the start of the cabinet manufacturing process helps align manufacturing flow, packaging, and customer expectations. At Casta Cabinetry, both framed and frameless systems are supported using precision CNC workflows, dowel and cam joinery, and customizable surface finishing.
5. Customization for Brands & Contractors
Customization plays a central role in the cabinet manufacturing process—especially for cabinet brands, contractors, and multi-site developers who require flexibility across styles, packaging, and branding. Casta Cabinetry’s workflow is designed to adapt to each client’s unique business model, helping them differentiate their offerings without disrupting timelines or budgets.
5.1 OEM Branding for Private Label Growth
In today’s market, visibility matters. That’s why the cabinet manufacturing process at Casta integrates OEM branding directly into production—allowing clients to elevate their product identity.
- Logo Etching or Printing: Apply your logo to drawer sides, back panels, or inside cabinet doors.
- QR Code Labeling: Unique SKUs printed with QR codes enable easier tracking in warehouses, across job sites, and during after-sale service.
- Custom Instructions & Documentation: Include branded manuals, spec sheets, or color booklets tailored to your audience.
This level of personalization supports cabinet and furniture brands building their own retail or DTC (direct-to-consumer) presence, whether online or in showrooms.
5.2 Modular Engineering for Diverse Project Needs
A modern kitchen cabinet manufacturing process must go beyond standard box sizes. With regional appliance differences, custom layouts, and project-specific clearance needs, flexibility is no longer optional—it’s essential. Casta’s modular engineering workflow is built to handle this complexity without slowing production or increasing rework.
- 32mm Hole System Compatibility
Standardized shelf and drawer placements support flexible layouts and hardware adjustments. This system ensures alignment with European hinges, shelf pins, and aftermarket components—especially important for frameless configurations.
- Pre-Mounted Custom Hardware
Whether your project requires BLUM soft-close runners, Häfele lift-up systems, or specialty pull-outs, Casta pre-installs hardware based on your appliance schedule. This includes allowances for non-standard ovens, microwaves, dishwashers, and built-in refrigerators that deviate from typical North American sizes.
- CAD-to-Production Support
Submit your kitchen layout or appliance specs in PDF, SketchUp, or CAD format—Casta engineers will return fully nested parts with dimension-accurate 3D mockups. This step ensures layout-fit before manufacturing begins, saving costly corrections later.
By embedding flexibility into every step of the kitchen cabinet manufacturing process, Casta enables smoother installations and better end-user satisfaction—whether you're furnishing a 500-unit apartment block or a luxury condo with bespoke appliances.
5.3 Flexible Packaging for Multi-Site Installs
Logistics shouldn’t disrupt a project timeline. That’s why packaging is tailored to each customer’s delivery and installation process—making the cabinet manufacturing process complete from production floor to job site.
- Unit- or Floor-Based Labeling: Every KD or assembled cabinet is labeled with project-specific identifiers, making unloading and installation intuitive.
- Mixed SKU Container Loading: Combine multiple finishes, sizes, or layouts in one shipment without delay.
- Phased Shipment Options: For multi-phase projects, Casta can split production across containers and timeframes—ideal for developers managing large job sites or staggered timelines.
Learn more: Best custom cabinet manufacturers
Whether you're outfitting 10 townhomes or 1,000 apartment units, customization in packaging and delivery ensures that cabinets arrive exactly when—and how—you need them.
Casta’s approach to customization proves that a flexible cabinet manufacturing process doesn’t have to compromise on precision, timing, or quality. Whether you're a growing brand or a national contractor, our systems adapt to your vision—every step of the way.
6. Certifications & Health Standards
At Casta Cabinetry, every stage of the cabinet manufacturing process is aligned with internationally recognized certifications. These standards aren't just checkboxes—they’re essential for North American importers, contractors, and furniture brands looking to ensure safety, compliance, and long-term durability.
6.1 CARB Phase 2 Compliance
The California Air Resources Board (CARB) Phase 2 standard regulates formaldehyde emissions from composite wood products, including MDF, particleboard, and hardwood plywood. Every cabinet panel used in Casta’s production is CARB P2 certified.
- Why It Matters: Required for distribution across the U.S., especially in California, New York, and other states with strict emission laws.
- In the Manufacturing Process: Testing and verification begin at material sourcing and continue during lamination and finishing.
This ensures that cabinets remain safe for indoor air quality over the long term.
6.2 E1 Emission Standard for European & Canadian Markets
In addition to CARB, Casta complies with the E1 emission standard, which regulates volatile organic compounds (VOCs) in wood products. This is a must-have for clients distributing in Canada and the EU.
- Tested Emission Limit: ≤ 0.124 mg/m³ of formaldehyde.
- Process Control: All boards are batch-tested and tracked by barcode through the entire cabinet manufacturing process—including cutting, banding, and assembly.
This dual-certification system (CARB + E1) provides peace of mind for brands selling into multiple regions.
6.3 FSC® Mix Credit Certification
Sustainability is increasingly part of project requirements. That’s why Casta offers FSC Mix-Credit cabinets on request—sourced from responsibly managed forests under the Forest Stewardship Council guidelines.
- Where It Applies: Retail programs, LEED® projects, government contracts, and green building certifications.
- Supply Chain Transparency: Chain-of-custody is documented throughout the kitchen cabinet manufacturing process, from raw wood input to final shipment.
Brands that prioritize ethical sourcing or need to meet green building targets can confidently promote FSC-backed collections.
6.4 Third-Party Verification & Documentation
Casta provides full documentation with every shipment, including:
- Third-party formaldehyde test reports (CARB/E1)
- FSC chain-of-custody certifications (on request)
- Coating MSDS (Material Safety Data Sheets)
- Bill of Lading, Fumigation Certificates, and Origin Docs
All certifications are aligned to the custom cabinet manufacturing process, ensuring products are approved at customs, pass jobsite inspections, and meet client safety expectations.
In an era of increasing regulation, sourcing from a factory that integrates health standards into the cabinet manufacturing process is not just smart—it’s essential. With Casta, you get verified materials, clean indoor air performance, and documentation that clears port and project requirements without delays.
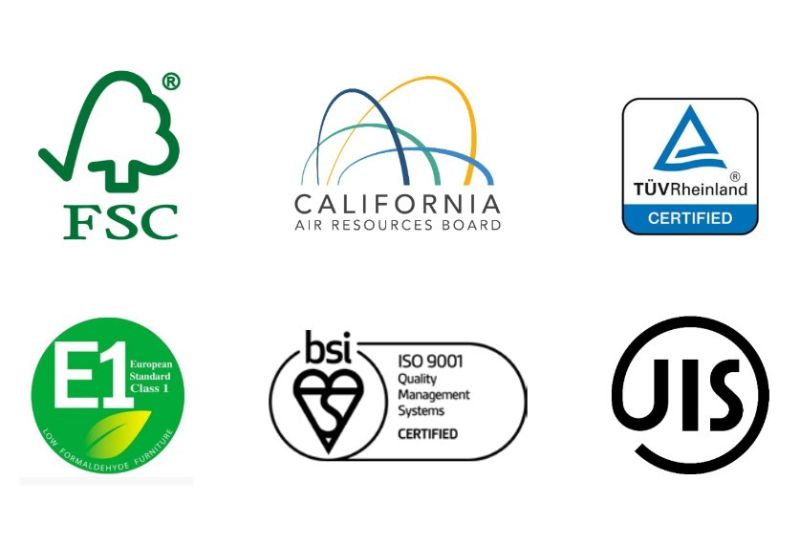
7. Why Work With Casta Cabinetry Instead of China or U.S. Suppliers
Choosing the right supplier is as critical as choosing the right materials. In today's global market, the reliability of your manufacturing partner directly impacts your timeline, quality control, and brand reputation. Casta Cabinetry offers a unique value proposition—combining the cost advantages of Southeast Asia with European-grade precision and export-ready support—making them an ideal long-term partner for North American buyers. Here's how they compare to typical manufacturers in China and the U.S.
7.1 Strategic Advantage in Cost, Machinery, and Documentation
Feature | Casta (Vietnam) | China | U.S. |
Cost | Low labor and overhead = competitive pricing | Moderate labor costs, rising tariffs | High labor and facility costs |
Machinery | HOMAG, Biesse, SCM (EU brands) | Mixed tiers—some outdated systems | Typically high-end automation |
Quality Control | Strict 3-stage QC integrated into ERP | Varies by supplier | Consistent, but at higher unit cost |
Certifications | Complete set: CARB P2, E1, FSC, MSDS | Not always consistent across suppliers | Always available, but with higher pricing |
Support | Fluent English engineers & sales staff | May require sourcing agent or translator | Native English support |
What sets Casta apart is how these advantages are built into every step of the cabinet manufacturing process—from raw board sourcing to export packaging and post-sale support.
7.2 Automation = Precision and Volume
The core of Casta’s competitiveness lies in its high level of automation. The entire cabinet manufacturing process is controlled by advanced European equipment, allowing for ultra-tight tolerances and mass production without losing quality.
- Tolerance Accuracy: ±0.2 mm, even across multi-container batch orders.
- Machinery Used: HOMAG CNC routers, Biesse edgebanders, SCM panel saws—identical to those used by top European brands.
- Factory Output: Over 200 full containers/month across kitchen, vanity, and closet systems.
This level of output makes Casta an ideal choice for large-scale residential, hospitality, or commercial projects where consistency across thousands of units is essential. Their automation ensures your project stays on schedule—and your end customers receive uniform, precision-cut cabinets every time.
Learn more: Casta’s Ideal Custom Cabinets
7.3 Designed for Export to North America
One of the biggest challenges in working with overseas cabinet suppliers is communication and export readiness. Casta eliminates those pain points by integrating international compliance, native-language support, and a responsive export team into the cabinet manufacturing process.
- English-Speaking Sales & Engineering Team: No need for sourcing agents or translation services—your specs and questions are understood the first time.
- Integrated QC + CAD Review: Each design file is reviewed for feasibility and optimized for automated production. Your custom specs are translated directly into CNC-compatible files, avoiding errors or miscommunication.
- Sample Doors in Under 10 Days: Before full production, you receive physical samples that reflect exact color, finish, and construction—so you can align your team and stakeholders confidently.
Exporting to the U.S. or Canada? Casta’s team handles:
- All necessary documentation: CARB P2, FSC, E1, MSDS, Fumigation Certs, and more.
- Custom packaging optimized for sea freight and local handling.
- Coordination with your U.S. receiving warehouse or port agent.
For contractors, developers, and cabinet brands seeking long-term reliability, working with Casta Cabinetry means getting a world-class cabinet manufacturing process—with fewer delays, fewer defects, and more predictability. You don’t have to compromise between price and performance. Casta gives you both.
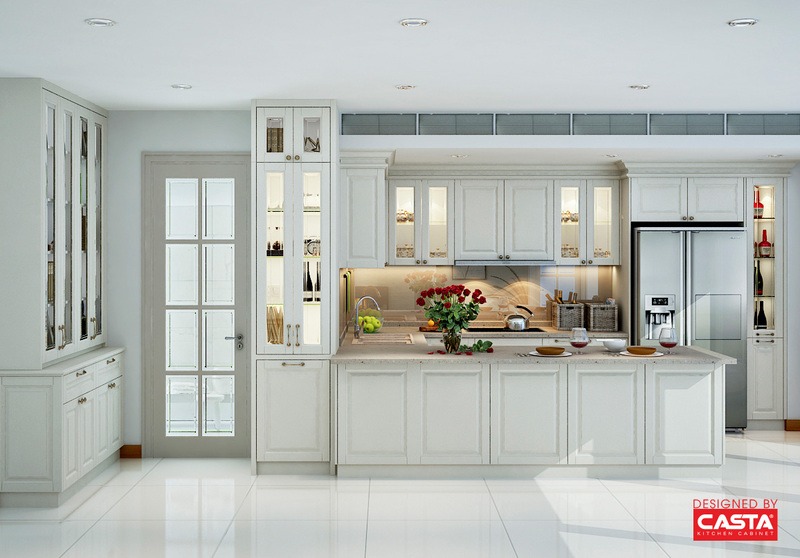
8. Conclusion
Whether you’re sourcing kitchen cabinets for a build-to-rent project or launching a modern flat-pack line, understanding the cabinet manufacturing process unlocks greater control over cost, quality, and lead time. With facilities that rival Western factories and pricing that beats most Chinese OEMs, Casta Cabinetry is positioned to become a long-term strategic partner for North American buyers.
By aligning automation with health certification and export logistics, Casta turns cabinet manufacturing into a streamlined, scalable, and compliant process—from CAD to container.
9. FAQ
Can I send my own cabinet drawings?
Are frameless cabinets KD or assembled?
What’s the MOQ?
Do you offer private label?
Are Casta’s cabinets suitable for commercial jobs?
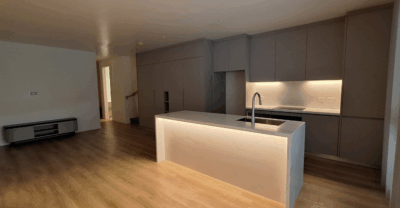
Where to Buy Manufactured Home Cabinet Doors
Cabinet is one of the most critical components in manufactured homes, and selecting the right manufactured home cabinet ...
08/29/2025 | David Nguyen
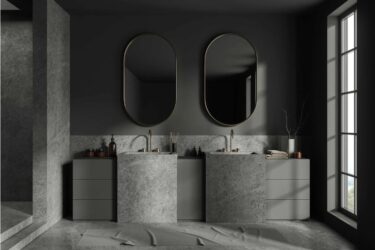
Where to Source Wholesale Bathroom Vanities: Top Suppliers ...
Sourcing wholesale bathroom vanities isn’t just about slashing per-unit costs—it’s about streamlining your entire projec...
08/23/2025 | David Nguyen
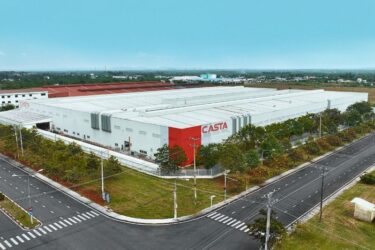
Best Furniture Manufacturer in Vietnam
A furniture manufacturer in Vietnam offers North American contractors and cabinet brands a reliable solution for high-vo...
08/21/2025 | David Nguyen
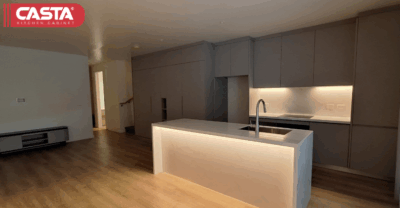
Next-Gen Cabinets for Manufactured Homes: Trends, Where to B...
In recent years, the role of cabinets for manufactured homes has evolved from basic “builder grade” components into high...
08/15/2025 | David Nguyen
Contact us
Casta is always ready to listen and answer all customers' questions
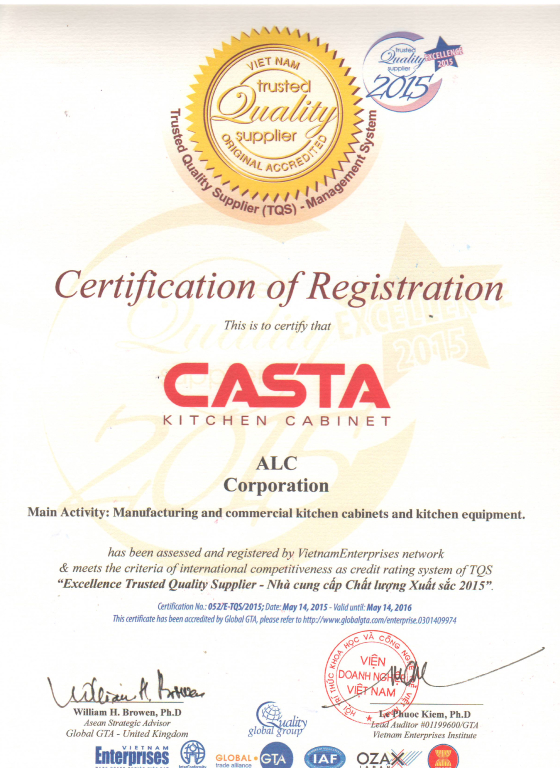
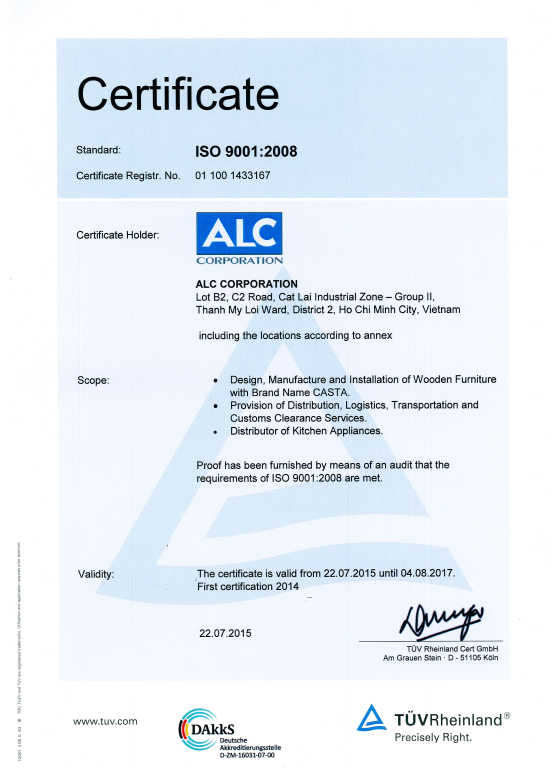
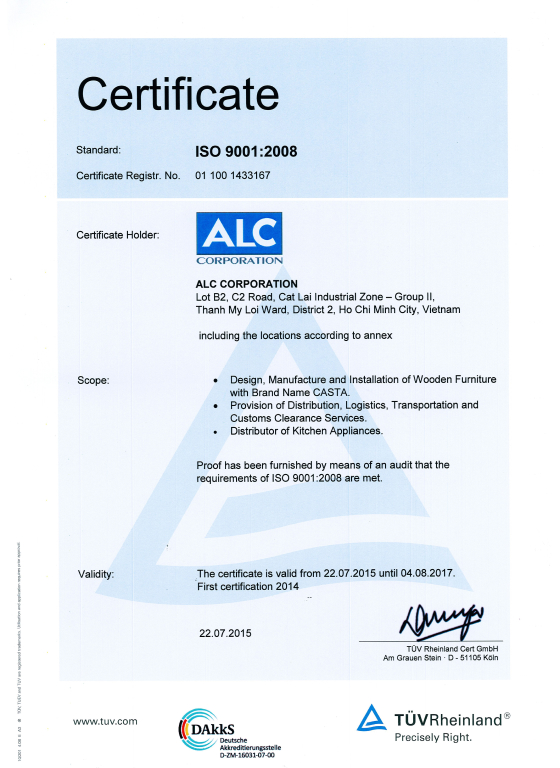